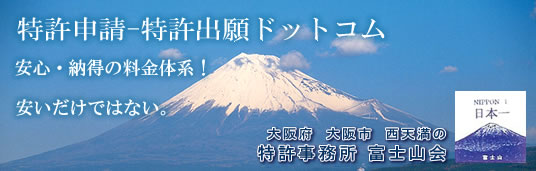
塩素化有機化合物分解用触媒
塩素化有機化合物分解用触媒
(書誌+要約+請求の範囲)
(19)【発行国】日本国特許庁(JP)
【公報種別】再公表特許(A1)
(11)【国際公開番号】WO00/16898
【発行日】平成13年12月4日(2001.12.4)
(54)【発明の名称】塩素化有機化合物分解用触媒
(51)【国際特許分類第7版】
B01J 23/52 ZAB
23/66
23/89
【FI】
B01J 23/52 ZAB A
23/66 A
23/89 A
【審査請求】未請求
【予備審査請求】有
【全頁数】48
【出願番号】特願2000−573851(P2000−573851)
(21)【国際出願番号】PCT/JP99/05099
(22)【国際出願日】平成11年9月17日(1999.9.17)
(43)【国際公開日】平成12年3月30日(2000.3.30)
(31)【優先権主張番号】特願平10−268390
(32)【優先日】平成10年9月22日(1998.9.22)
(33)【優先権主張国】日本(JP)
(31)【優先権主張番号】特願平11−175728
(32)【優先日】平成11年6月22日(1999.6.22)
(33)【優先権主張国】日本(JP)
(81)【指定国】EP(AT,BE,CH,CY,DE,DK,ES,FI,FR,GB,GR,IE,IT,LU,MC,NL,PT,SE),JP,US
(71)【出願人】
【氏名又は名称】大阪瓦斯株式会社
【住所又は居所】大阪府大阪市中央区平野町四丁目1番2号
(72)【発明者】
【氏名】梶川 修
【住所又は居所】大阪府大阪市中央区平野町四丁目1番2号 大阪瓦斯株式会社内
(72)【発明者】
【氏名】前田 武士
【住所又は居所】大阪府大阪市中央区平野町四丁目1番2号 大阪瓦斯株式会社内
(72)【発明者】
【氏名】佐藤 富徳
【住所又は居所】大阪府大阪市中央区平野町四丁目1番2号 大阪瓦斯株式会社内
(72)【発明者】
【氏名】王 祥生
【住所又は居所】京都府京都市下京区中堂寺南町17 株式会社関西新技術研究所内
(72)【発明者】
【氏名】川瀬 昇
【住所又は居所】京都府京都市下京区中堂寺南町17 株式会社関西新技術研究所内
(74)【代理人】
【弁理士】
【氏名又は名称】市川 恒彦
(57)【要約】
粒子態やガス態などの各種の塩素化有機化合物に対する分解活性が高い触媒である。この触媒は、担体と、当該担体に担持された金元素からなる第1触媒成分と、当該担体に担持された、マグネシウム、アルミニウム、ケイ素、チタン、マンガン、鉄、コバルト、ニッケル、銅、亜鉛、イットリウム、ジルコニウム、ニオブ、モリブデン、インジウム、スズ、ランタンおよびセリウムからなる元素群から選ばれた少なくとも1種の元素の酸化物からなる第2触媒成分とを含んでいる。ここで用いられる担体は、好ましくは耐酸化性を有するものであり、また、比表面積が少なくとも100m2/gでありあつ平均細孔径が少なくとも10オングストロームのものである。
【特許請求の範囲】
【請求項1】担体と、 前記担体に担持された金元素からなる第1触媒成分と、 前記担体に担持された、マグネシウム、アルミニウム、ケイ素、チタン、マンガン、鉄、コバルト、ニッケル、銅、亜鉛、イットリウム、ジルコニウム、ニオブ、モリブデン、インジウム、スズ、ランタンおよびセリウムからなる元素群から選ばれた少なくとも1種の元素の酸化物からなる第2触媒成分と、を含む塩素化有機化合物分解用触媒。
【請求項2】前記担体が耐酸化性を有するものである、請求項1に記載の塩素化有機化合物分解用触媒。
【請求項3】前記担体がシリカ、アルミナ、ゼオライトおよび活性白土からなる群から選ばれた少なくとも1種である、請求項2に記載の塩素化有機化合物分解用触媒。
【請求項4】前記担体は、比表面積が少なくとも100m2/gでありかつ平均細孔径が少なくとも10オングストロームのものである、請求項1に記載の塩素化有機化合物分解用触媒。
【請求項5】前記担体が繊維状態および粒子状態のうちの少なくとも一つの形態である、請求項4に記載の塩素化有機化合物分解用触媒。
【請求項6】前記第1触媒成分が前記担体100g当たりに0.05〜5g、前記第2触媒成分が前記担体100g当たりに1〜25gそれぞれ担持されており、かつ前記第2触媒成分に対する前記第1触媒成分のモル比が0.005〜0.2に設定されている、請求項1に記載の塩素化有機化合物分解用触媒。
【請求項7】担体に対し、金元素に転化可能な金化合物と、マグネシウム、アルミニウム、ケイ素、チタン、マンガン、鉄、コバルト、ニッケル、銅、亜鉛、イットリウム、ジルコニウム、ニオブ、モリブデン、インジウム、スズ、ランタンおよびセリウムからなる第1元素群から選ばれた少なくとも1種の元素の酸化物に転化可能な前駆体とを担持させるための工程と、 前記金化合物および前記前駆体をそれぞれ前記金元素および前記酸化物に転化する工程と、を含む塩素化有機化合物分解用触媒の製造方法。
【請求項8】前記金化合物および前記前駆体がそれぞれ金水酸化物および前記第1元素群から選ばれた少なくとも1種の元素の水酸化物である、請求項7に記載の塩素化有機化合物分解用触媒の製造方法。
【請求項9】前記金化合物および前記前駆体をそれぞれ前記金元素および前記酸化物に転化する工程が、 前記金化合物および前記前駆体を担持した前記担体を250〜700℃の温度範囲の不活性ガス雰囲気中および空気中のうちから選択された1つの雰囲気中で熱処理する工程と、 熱処理された前記担体を200〜600℃の温度範囲の還元性ガス雰囲気中でさらに熱処理する工程と、を含む請求項8に記載の塩素化有機化合物分解用触媒の製造方法。
【請求項10】前記担体は、無機酸の3%〜飽和濃度水溶液中で室温から沸騰温度までの温度範囲で煮沸処理した後に水洗浄して乾燥する前処理工程、およびその100g当たりに対して鉄、ニッケル、ルテニウム、ロジウム、パラジウムおよび白金からなる第2元素群から選ばれた少なくとも1種の元素を0.01〜5g分散させた後に300〜700℃の還元性ガス雰囲気中で触媒エッチング処理する前処理工程のうちの少なくとも一つの前処理工程により予め前処理されている、請求項7に記載の塩素化有機化合物分解用触媒の製造方法。
【請求項11】前記無機酸が硝酸、塩酸、フッ化水素酸、硫酸およびリン酸からなる群から選ばれた少なくとも1種である、請求項10に記載の塩素化有機化合物分解用触媒の製造方法。
詳細な説明
【発明の詳細な説明】
技術分野 本発明は、分解用触媒、特に、塩素化有機化合物分解用触媒に関する。
背景技術 産業廃棄物や一般家庭ごみなどを処理するための焼却施設、石炭発電施設、製鋼施設、金属精錬施設などから発生する排気ガス中には、ダイオキシン類、ポリクロロビフェニル(PCB)、クロロフェノール、クロロベンゼンなどの塩素化有機化合物が含まれている。
ここで、ダイオキシン類は、ポリ塩化ジベンゾ・パラ・ダイオキシン類(PCDDs)やポリ塩化ジベンゾフラン類(PCDFs)の総称であり、周知の如く極めて毒性の強い環境汚染物質であるが、その中でも四塩化ジベンゾダイオキシン(T4CDDs)は特に最強の毒性物質として知られている。一方、ポリクロロビフェニル、クロロフェノール、クロロベンゼンなどの塩素化有機化合物は、ダイオキシン類に比べて毒性は弱いが、一定の条件下、例えば、焼却炉内でフライアッシュ中の種々の元素を触媒として排気ガスの温度範囲でダイオキシン類に変換されやすいことが判明しているため、ダイオキシン類と同様に環境汚染物質として認識されている。このため、環境保全の観点から、上述のような各種の塩素化有機化合物を排気ガス中から除去する必要性が急速に高まりつつある。
ところで、排気ガス中から塩素化有機化合物を除去する手法として、主に2通りの手法が提案されている。一つは、活性炭などの吸着材に塩素化有機化合物を吸着させる手法であり、他方は触媒を用いて塩素化有機化合物を分解する手法である。しかし、吸着材を用いる手法は、大量の吸着材を用いなければ排気ガス中に含まれる微量の塩素化有機化合物を効果的に吸着除去することができないので、実施コストが高くなり、また、使用済みの吸着材の廃棄処分方法や再生処理方法などが確立しない限り実用性に疑問がある。
このため、触媒を用いて塩素化有機化合物を分解する手法が注目されており、そのための触媒が多数提案されている。例えば、五酸化バナジウム、酸化タングステン、チタニアからなる脱硝触媒やその脱硝触媒に白金を担持させた触媒(特開平7−75720号公報、特開平2−35914号公報参照)、シリカ・ボリア・アルミナ複合酸化物およびアルミナに対するシリカのモル比が30以上のゼオライトのうちの少なくとも1種に対してその1リットル当たり白金、パラジウムおよびイリジウムからなる群から選ばれた少なくとも1種類の元素またはその酸化物を0.1〜10g担持させた触媒(特開平7−163877号公報参照)、バナジウム酸化物と、イットリウム、ホウ素および鉛からなる群から選ばれた少なくとも1種の元素の酸化物とを含む混合酸化物触媒(特開平9−29066号公報参照)などが知られている。
しかしながら、これらの触媒は、塩素化有機化合物をある程度は分解することができるものの、その能力は小さく、塩素化有機化合物に対して真に有効な分解触媒とは言い難い場合が多い。特に、排気ガス中には、粒子態およびガス態の塩素化有機化合物が含まれているが、粒子態の塩素化有機化合物は、上述の触媒で分解されにくい。
本発明の目的は、塩素化有機化合物に対する分解活性が高い触媒を実現することにある。
発明の開示 本発明に係る塩素化有機化合物分解用触媒は、担体と、当該担体に担持された金元素からなる第1触媒成分と、当該担体に担持された、マグネシウム、アルミニウム、ケイ素、チタン、マンガン、鉄、コバルト、ニッケル、銅、亜鉛、イットリウム、ジルコニウム、ニオブ、モリブデン、インジウム、スズ、ランタンおよびセリウムからなる元素群から選ばれた少なくとも1種の元素の酸化物からなる第2触媒成分とを含んでいる。
ここで用いられる担体は、例えば、耐酸化性を有するものである。この担体は、例えば、シリカ、アルミナ、ゼオライトおよび活性白土からなる群から選ばれた少なくとも1種である。また、担体は、例えば、比表面積が少なくとも100m2/gでありかつ平均細孔径が少なくとも10オングストロームのものである。
なお、担体は、例えば、繊維状態および粒子状態のうちの少なくとも一つの形態である。
この塩素化有機化合物分解用触媒では、例えば、第1触媒成分が担体100g当たりに0.05〜5g、第2触媒成分が担体100g当たりに1〜25gそれぞれ担持されており、かつ第2触媒成分に対する第1触媒成分のモル比が0.005〜0.2に設定されている。
このような本発明の塩素化有機化合物分解用触媒は、担体上に上述のような第1触媒成分と第2触媒成分とを組み合わせて担持させているので、粒子態のものを含む各種の塩素化有機化合物に対して高い分解活性を発揮し得る。
本発明に係る塩素化有機化合物分解用触媒の製造方法は、担体に対し、金元素に転化可能な金化合物と、マグネシウム、アルミニウム、ケイ素、チタン、マンガン、鉄、コバルト、ニッケル、銅、亜鉛、イットリウム、ジルコニウム、ニオブ、モリブデン、インジウム、スズ、ランタンおよびセリウムからなる第1元素群から選ばれた少なくとも1種の元素の酸化物に転化可能な前駆体とを担持させるための工程と、金化合物および前記前駆体をそれぞれ前記金元素および前記酸化物に転化する工程とを含んでいる。
ここで、前記金化合物および前記前駆体は、例えば、それぞれ金水酸化物および第1元素群から選ばれた少なくとも1種の元素の水酸化物である。
また、前記金化合物および前記前駆体をそれぞれ前記金元素および前記酸化物に転化する工程は、例えば、前記金化合物および前記前駆体を担持した担体を250〜700℃の温度範囲の不活性ガス雰囲気中および空気中のうちから選択された1つの雰囲気中で熱処理する工程と、熱処理された担体を200〜600℃の温度範囲の還元性ガス雰囲気中でさらに熱処理する工程とを含んでいる。
なお、担体は、例えば、無機酸の3%〜飽和濃度水溶液中で室温から沸騰温度までの温度範囲で煮沸処理した後に水洗浄して乾燥する前処理工程、およびその100g当たりに対して鉄、ニッケル、ルテニウム、ロジウム、パラジウムおよび白金からなる第2元素群から選ばれた少なくとも1種の元素を0.01〜5g分散させた後に300〜700℃の還元性ガス雰囲気中で触媒エッチング処理する前処理工程のうちの少なくとも一つの前処理工程により予め前処理されている。この際に用いられる無機酸は、例えば、硝酸、塩酸、フッ化水素酸、硫酸およびリン酸からなる群から選ばれた少なくとも1種である。
このような製造方法は、担体に対して金元素と所定の元素の酸化物とを担持させているので、粒子態のものを含む各種の塩素化有機化合物に対して高い分解活性を発揮し得る塩素化有機化合物分解用触媒を製造することができる。
本発明の他の目的および効果は、以下の詳細な説明から明らかになるであろう。
発明の詳細な説明 本発明の塩素化有機化合物分解用触媒は、各種の塩素化有機化合物を分解するためのものであり、担体と、当該担体に担持された第1触媒成分および第2触媒成分とを含んでいる。ここで、第1触媒成分および第2触媒成分のそれぞれは、通常、ランダムに分散した状態で担体上に担持されている。
本発明で用いられる担体は、各種の触媒成分を担持させるために通常用いられる公知の各種のものであり、形状・形態が特に限定されるものではなく、例えば、繊維状態であってもよいし、粒子状態であってもよい。また、繊維状態のものと粒子状態のものとの混合物であってもよい。さらに、繊維状態、粒子状態またはこれらの混合物を用いて所望の形状(例えばハニカム形状)に成形された成形体状であってもよい。なお、繊維状態の担体は、被処理気体の圧損が大きくなるため、適宜所望の形状に成形して用いるのが好ましいが、粒子状態の担体は、被処理気体の圧損が小さいので、成形せずにそのままの状態で利用することができる。したがって、本発明の塩素化有機化合物分解用触媒は、粒子状態の担体を用いている場合、例えば焼却施設の排気ガス分解処理塔中にそのまま充填するだけで、排気ガスの速やかな流通を確保しつつ、排気ガス中に含まれるガス態や粒子態の各種の塩素化有機化合物を効果的に分解することができる。
ここで、繊維状態の担体としては、例えば炭素繊維や活性炭素繊維を挙げることができる。ここで利用可能な炭素繊維は、公知の各種の炭素前駆体を紡糸し、これを不融化または炭素化したものである。また、活性炭素繊維は、公知の各種の炭素前駆体を紡糸し、これを不融化または炭素化するとともに賦活したものである。因みに、炭素繊維および活性炭素繊維として好ましいものは、ポリアクリロニトリル系、レーヨン系、ピッチ系、リグニン−ポバール系からなる群から選ばれた少なくとも1種のもの、すなわち、当該群から選ばれた1種のものまたは2種以上の混合物である。活性炭素繊維としてこのようなものを用いた場合は、その比表面積および平均細孔径が後述するような好ましい範囲に設定され易く、ガス態および粒子態の両方の塩素化有機化合物を効果的に分解することができる。
一方、粒子状態の担体としては、例えば、シリカ、アルミナ、粒状炭、粒状活性炭、ゼオライト、活性白土などを挙げることができる。このような粒子状態の担体は、2種以上のものが混合して用いられてもよい。これらの粒子状態の担体のうち、粒状活性炭、特に薬品賦活により得られる粒状活性炭は、比表面積が大きく、触媒成分を表面に分散し易いという特徴を有している。なお、ここで言う粒状活性炭は、粒子径が小さな粉末状活性炭を含む概念である。
因みに、粒子状態の担体の平均粒径は、特に限定されるものではないが、被処理気体の圧損を考慮した場合、通常、0.1〜20mmが好ましく、3〜10mmがより好ましい。
本発明で担体として用いられる粒子状態のシリカとしては、例えば、富士ディビソン株式会社の商品名“シリカゲルA”、“シリカゲルB”および“シリカゲルRD”を挙げることができる。また、粒子状態のアルミナとしては、例えば、水澤化学株式会社の商品名“Neobead C”、“Neobead D”および“Neobead SA”を挙げることができる。さらに粒状活性炭としては、例えば、武田薬品工業株式会社の商品名“CarbTech−A”、“CarbTech−B”、“WH2C−20/48”、“WH2C−8/32”、“WH2C−28/70SS”、“G2X−4/6−1”および“G2C−4/8”を挙げることができる。さらに、粉末状活性炭としては、例えば、大阪瓦斯株式会社の商品名“M−24”、“M−30”および“M−38”並びに二村化学工業株式会社の商品名“薬品賦活活性炭”および“水蒸気賦活活性炭”を挙げることができる。
本発明の触媒で用いられる担体として好ましいものは、耐酸化性を有するもの、例えば、シリカ、アルミナ、ゼオライト、活性白土またはこれらの任意の組み合わせによる混合物である。また、活性炭素繊維等の炭素系の担体に対してポリシランやシロキサンをコーティングして熱処理したものも耐酸化性を発揮し得る。このような担体を用いた場合は、それら自体が酸化されにくく安定であるので、長期間に渡って安定な分解活性を示す寿命の長い塩素化有機化合物分解用触媒を実現することができる。因みに、このような耐酸化性を有する担体は、通常、熱分析(TG分析)を実施した場合において、150℃以上の温度範囲に相転移点を有するもの、または250℃の酸化性雰囲気中で1ヶ月放置した場合でも重量減少率が0.3%以下のものである。
また、本発明の触媒で用いられる担体として好ましいものは、比表面積が少なくとも100m2/g(すなわち、100m2/g以上)でありかつ平均細孔径が少なくとも10オングストローム(すなわち、10オングストローム以上)の多孔質状のものである。担体の比表面積が100m2/g未満でありかつ平均細孔径が10オングストローム未満の場合は、担体の単位重量当たりのガス処理可能量が少なくなるため、塩素化有機化合物を含む排気ガスなどの被処理気体を効率的にかつ効果的に処理しにくくなるおそれがある。また、粒子態の塩素化有機化合物が吸着されにくくなるおそれがあり、そのような塩素化有機化合物を効果的に分解処理するのが困難になるおそれがある。
なお、担体の比表面積は少なくとも300m2/gであるのがより好ましく、少なくとも500m2/gであるのがさらに好ましい。また、平均細孔径は少なくとも14オングストロームであるのがより好ましく、少なくとも18オングストロームであるのがさらに好ましい。因みに、上述の比表面積は、窒素吸着法に従って求めたBET比表面積である。一方、平均細孔径は、窒素吸着法により測定したBET比表面積と細孔容積の値とから算出した値である。上述の各種の担体が混合物として用いられる場合、上述の比表面積や平均細孔径は、混合物全体の値として設定されていればよい。
また、上述のような多孔質状の担体を用いる場合、その細孔容積は、上述の比表面積および平均細孔径により決定され得るが、通常、少なくとも0.15cc/g(すなわち、0.15cc/g以上)に設定されているのが好ましく、少なくとも0.50cc/gに設定されているのがより好ましい。なお、ここで言う細孔容積は、窒素吸着法に従って求めることができる全細孔容積である。
本発明で用いられる上述の担体は、第1触媒成分および第2触媒成分の担持量を増大させることを目的として、適宜表面処理されていてもよい。表面処理としては、例えば、後述するような酸の水溶液による煮沸処理や触媒エッチング処理を挙げることができる。
上述のような担体に担持される第1触媒成分は、金元素、特に金の微粒子からなる。担体に担持される第1触媒成分の量は、通常、担体100g当たり0.05〜5g、好ましくは0.1〜3g、より好ましくは0.5〜2gに設定される。この担持量が0.05g未満の場合は、本発明の触媒が触媒活性、すなわち塩素化有機化合物の分解活性を殆ど示さなくなるおそれがある。逆に、5gを超えると、金の粒子のサイズが大きくなり、本発明の触媒の触媒活性が極端に低下するおそれがある。
なお、第1触媒成分は、通常、平均粒径が20nm以下の微粒子状で担体に担持されているのが好ましい。
一方、担体に担持される第2触媒成分は、マグネシウム、アルミニウム、ケイ素、チタン、マンガン、鉄、コバルト、ニッケル、銅、亜鉛、イットリウム、ジルコニウム、ニオブ、モリブデン、インジウム、スズ、ランタンおよびセリウムからなる元素群(第1元素群)から選ばれた元素の酸化物である。この第2触媒成分は、当該元素群から選ばれた元素の酸化物が2種以上混合されたものであってもよい。
上述の酸化物は、上述の元素群に含まれる元素の各種の酸化物であって特に限定されるものではなく、例えば、酸化マグネシウム(MgO)、酸化アルミニウム(Al2O3)、酸化ケイ素(SiO、SiO2)、酸化チタン(TiO、Ti2O3、TiO2)、酸化マンガン(MnO、Mn3O4、Mn2O3、MnO2、MnO3、Mn2O7)、酸化鉄(FeO、Fe3O4、Fe2O3)、酸化コバルト(CoO、Co2O3、Co3O4、CoO2)、酸化ニッケル(NiO、Ni3O4、NiO2)、酸化銅(CuO2、CuO)、酸化亜鉛(ZnO)、酸化イットリウム(Y2O3)、酸化ジルコニウム(ZrO2)、酸化ニオブ(NbO、Nb2O3、NbO2、Nb2O5)、酸化モリブデン(MoO、MoO2、Mo2O5、MoO3)、酸化インジウム(In2O3)、酸化スズ(SnO、SnO2)、酸化ランタン(La2O3)、酸化セリウム(CeO2、Ce2O3)を挙げることができる。このうち、第1触媒成分である金の微粒子の分散性を高め、また、本発明の触媒の低温酸化分解活性を高めることができることから、MgO、Al2O3、SiO2、TiO2、MnO、Fe2O3、Co3O4、NiO、CuO、ZnO、Y2O3、ZrO2、Nb2O5、MoO3、In2O3、SnO2、La2O3およびCeO2を用いるのが好ましい。
担体に担持される第2触媒成分の量は、通常、担体100g当たり1〜25g、好ましくは5〜25g、より好ましくは12〜20gに設定される。この担持量が1g未満の場合は、本発明の触媒が触媒活性を殆ど示さなくなるおそれがある。逆に、25gを超えると、担体から第2触媒成分が分離してしまうおそれがある。
担体に担持される上述の第1触媒成分と第2触媒成分との比率は、通常、第2触媒成分に対する第1触媒成分のモル比が0.005〜0.2、好ましくは0.01〜0.2、より好ましくは0.03〜0.15になるよう設定する。このモル比が0.005未満の場合は、本発明の触媒が触媒活性を殆ど示さなくなるおそれがある。逆に、0.2を超える場合は、第1触媒成分である金の微粒子のサイズが大きくなり、本発明の触媒の触媒活性が極端に低下するおそれがある。
次に、本発明に係る上述の塩素化有機化合物分解用触媒の製造方法について説明する。本発明の塩素化有機化合物分解用触媒は、基本的に担体に対して第1触媒成分および第2触媒成分を担持させることにより製造することができるが、担体は、触媒成分が担持されやすいようにするために予め表面化学状態を改質しておくのが好ましい。
ここで、担体の表面化学状態を改質するための方法としては、例えば酸の水溶液中で担体を煮沸処理する方法や担体に対して所謂触媒エッチング処理を施す方法などを採用することができる。因みに、触媒エッチング処理とは、担体に所定の触媒を分散させ、その触媒の作用により担体の既存の細孔を拡大したり担体に新たな細孔を形成する処理をいう。
このような表面改質処理が施された担体は、第1触媒成分および第2触媒成分の付着性が改善され、これらの触媒成分の担持量を高めることができる。また、触媒エッチングを施した場合は、担体の比表面積、細孔容積および平均細孔径を増大させることもできるので、粒子態の塩素化有機化合物の吸着性を高め、その分解特性をより高めることができる。
例えば、担体としてピッチ系活性炭素繊維(平均繊維径=14.0μm、BET比表面積=1,920m2/g、平均細孔径=19.01オングストローム)を用い、当該担体に対し、第1触媒成分として金を、また、第2触媒成分として酸化鉄(Fe2O3)と酸化ランタン(La2O3)との混合物を、それぞれ炭酸ナトリウム水溶液を沈殿剤とする共沈殿法により担持させる場合、ピッチ系活性炭素繊維に対して酸の水溶液を用いた煮沸処理を実施しなければ、担持される触媒の総量はピッチ系活性炭素繊維100g当たり僅か2.5重量%である。これに対し、ピッチ系活性炭素繊維を30%硝酸水溶液の沸騰液中で2時間煮沸した場合は、担持される触媒の総量がピッチ系活性炭素繊維100g当たり13重量%になる。
一方、担体としてピッチ系活性炭素繊維(平均繊維径=14.0μm、BET表面積=1,920m2/g、平均細孔径=19.01オングストローム)を用い、当該担体に対し、第1触媒成分として金を、また、第2触媒成分として酸化マグネシウム(MgO)を、それぞれ炭酸ナトリウム水溶液を沈殿剤とする共沈殿法により担持させる場合、ピッチ系活性炭素繊維に対して触媒エッチング処理を施さなければ、担持される触媒の総量はピッチ系活性炭素繊維100g当たり僅か3.1重量%である。これに対し、ピッチ系活性炭素繊維に対して触媒としてのニッケルを0.5重量%分散してから500℃の水素雰囲気中で1時間エッチング処理を施した場合は、担持される触媒の総量がピッチ系活性炭素繊維100g当たり14.1重量%になる。
担体を酸の水溶液中で煮沸してその表面化学状態を改質する場合に用いられる酸の水溶液は、無機酸の水溶液である。ここで利用可能な無機酸としては、例えば硝酸、塩酸、フッ化水素酸、硫酸およびリン酸を挙げることができる。このような無機酸の水溶液は、2種以上の無機酸を混合して調製されたものであってもよい。また、無機酸の濃度は、通常、3%〜飽和濃度に設定するのが好ましいが、酸濃度を高く設定した方が通常はより良好な表面改質効果が得られる。
上述の酸の水溶液による担体の煮沸処理温度は、室温から酸の水溶液の沸騰温度の範囲に設定することができ、また、煮沸処理時間は、通常、1分以上に設定される。なお、煮沸処理温度は高い程、また、煮沸処理時間は長い程、より良好な表面改質効果が得られる。
上述のような煮沸処理工程の終了後、処理された担体を水洗浄する。ここでは、担体に付着している酸および酸処理による生成物をイオン交換水を用いて可能な限り洗い流すのが好ましい。担体に酸や酸処理による生成物が残存している場合は、本発明の塩素化有機化合物分解用触媒の分解活性が低下するおそれがある。
一方、担体に対して触媒エッチング処理を施す場合は、先ず、担体に対してエッチング触媒を分散させる。ここで用いられるエッチング触媒は、例えば、鉄、ニッケル、ルテニウム、ロジウム、パラジウムおよび白金からなる元素群(第2元素群)から選ばれた少なくとも1種の金属元素である。このようなエッチング触媒の分散量は、通常、担体100g当たりに対し0.01〜5g、好ましくは0.05〜2.0g、より好ましくは0.1〜1.0gに設定する。この分散量が0.01g未満の場合は、担体の表面を十分に改質できないおそれがある。逆に、5gを超える場合は、担体の表面全体が触媒エッチングされる場合があり、微細な表面凹凸が形成できないおそれがある。
なお、上述のエッチング触媒は、上述の金属元素の化合物として担体に分散されてもよい。この場合、上述の分散量は、金属元素換算の値である。なお、金属元素の化合物としては、例えば、酢酸塩、硝酸塩、硫酸塩などを用いることができる。
担体に対してエッチング触媒を分散させる方法としては、公知の各種の方法、例えば、含浸法、沈殿析出法、共沈殿法および蒸着法などの公知の金属分散方法を採用することができる。これらの分散方法は、上述の金属元素またはその化合物の種類に応じて適宜選択することができる。
上述のようにしてエッチング触媒が分散された担体をエッチングする際には、水素ガス、水素と不活性ガスとの混合ガスなどの還元性ガス雰囲気中において、300〜700℃(好ましくは350〜550℃)の温度範囲で担体を熱処理する。ここでの処理温度が300℃未満の場合は、担体に対して十分なエッチング効果を付与することができない場合がある。逆に、700℃を超える場合は、担体に分散させたエッチング触媒の微粒子が成長して焼結されてしまい、十分なエッチング効果が得られないおそれがある。ここでの処理時間は、通常、5分以上に設定するのが好ましいが、処理時間を長く設定する方が表面処理効果は高くなる。
担体に対して上述のような触媒エッチング処理を施した場合は、水添化活性を示す上述のエッチング触媒の作用の下で、担体の表面の酸素含有官能基や結合力の弱い炭素−炭素結合が水素等の還元性ガスと反応して一酸化炭素、二酸化炭素および水に転化され、生成したこれらの一酸化炭素、二酸化炭素および水が担体の表面から脱落する。これにより、担体の既存の細孔が拡大され、また、担体に新しい細孔が形成される。この結果、触媒エッチング処理された担体は、比表面積、細孔容積および平均細孔径が増大することになる。また、触媒エッチング処理後の担体の表面は、官能基分布および官能基濃度などの表面化学状態が処理前に比べて変化し、金属や金属化合物、すなわち、第1触媒成分および第2触媒成分の付着性が高まる。
担体に対する上述の煮沸処理および触媒エッチング処理は、いずれか一方のみが実施されてもよいし、両方が実施されてもよい。後者の場合、処理の順序は特に限定されるものではなく、煮沸処理をしてから触媒エッチング処理を施してもよいし、触媒エッチング処理の後に煮沸処理を施してもよい。但し、煮沸処理と触媒エッチング処理の両方の処理による表面改質効果をより効果的に引き出すためには、煮沸処理を施した後に触媒エッチング処理を施すのが好ましい。
なお、担体として比表面積および平均細孔径が上述のように設定された多孔質状のものを用いる場合、担体の比表面積および平均細孔径は、上述のような煮沸処理や触媒エッチング処理などの前処理前から上述のような範囲に設定されていてもよいし、上述のような前処理により上述のような範囲に設定されてもよい。すなわち、この種の担体は、次に説明する触媒成分の担持工程の前に比表面積および平均細孔径が上述の範囲に設定されていればよい。
次に、上述のようにして処理された担体に対し、第1触媒成分および第2触媒成分を担持させる。これらの触媒成分を担体に対して担持させる方法としては、公知の各種の方法、例えば、含浸法、析出沈殿担持法、共沈殿法およびクエン酸マグネシウム添加沈殿法等の化学的手法、並びに蒸着法、練込法等の物理的手法などの公知の金属または金属化合物の分散・担持方法を採用することができる。
また、担体に対して触媒成分を担持させる方法としては、第1触媒成分(即ち、金)に転化し得る金化合物および第2触媒成分(即ち、上述のような元素の酸化物)に転化可能な前駆体を担体に対して担持させた後、当該金化合物および前駆体をそれぞれ第1触媒成分および第2触媒成分に転化する方法を採用することもできる。
このような方法を採用する場合、例えば、金化合物としては金の水酸化物を用いることができ、前駆体としては第2触媒成分を構成する上述の元素の水酸化物を用いることができる。このような各種の水酸化物は、例えば上述の共沈殿法を採用すると、担体に対して付与することができる。
担体に対して付与された金の水酸化物および上述の元素の水酸化物は、通常、担体を不活性ガス雰囲気中で熱処理した後に必要に応じてさらに還元性ガス雰囲気中で熱処理を施すことにより、それぞれ目的とする金および上述の元素の酸化物に転化することができる。なお、担体が耐酸化性を有するシリカ、アルミナ、ゼオライト、活性白土またはこれらの混合物からなる場合、不活性ガス雰囲気中での熱処理工程は、空気中で実施されてもよい。
ここで、不活性ガス雰囲気中(または空気中)での熱処理は、担体に担持された上述の元素の水酸化物を目的とする酸化物に転化させ、第2触媒成分を形成するための工程である。ここでの熱処理温度は、通常、250〜700℃、好ましくは300〜450℃に設定する。この処理温度が250℃未満の場合は、上述の元素の水酸化物が目的とする酸化物に転化されにくくなるおそれがある。逆に、700℃を超える場合は、生成した金属酸化物が焼結され、本発明の触媒の活性が低下するおそれがある。また、熱処理時間は、通常、5分以上に設定するのが好ましい。熱処理時間が5分未満の場合は、上述の元素の水酸化物が目的とする酸化物に転化されにくい場合がある。
一方、還元性ガス雰囲気中での熱処理は、上述の不活性ガス雰囲気中(または空気中)での熱処理により同時に生成する金の酸化物を還元して金元素そのものに転化させ、第1触媒成分を形成するための工程である。ここでの熱処理温度は、通常、200〜600℃、好ましくは250〜400℃に設定する。この処理温度が200℃未満の場合は、金の酸化物が金元素に転化されにくい場合がある。逆に、処理温度が600℃を超える場合は、上述の不活性ガス雰囲気中(または空気中)での熱処理により生成した他の酸化物(すなわち、第2触媒成分)が金属元素に還元されてしまうおそれがある。また、熱処理時間は、金の酸化物を金元素に転化させやすくするために、通常5分以上に設定するのが好ましいが、処理時間が長くなり過ぎると、上述の不活性ガス雰囲気中(または空気中)での熱処理により生成した他の酸化物も対応する金属元素に同時に還元されてしまうおそれがある。従って、処理温度と処理時間は、金の酸化物のみが還元されて金元素に転化されるように、適切に調整する必要がある。
本発明の塩素化有機化合物分解用触媒は、上述のような担体に第1触媒成分と第2触媒成分とを担持させたものであるため、ダイオキシン類、並びにダイオキシン類に転化し得るポリクロビフェニル(PCB)、トリクロロエチレン、トリクロロエタン、ジクロロメタン、クロロフェノール類、クロロベンゼンおよびその他のハロゲン化炭化水素化合物などの塩素化有機化合物を効果的に酸化分解して無毒性の低分子化合物に転化することができる。
特に、本発明の塩素化有機化合物分解用触媒は、ガス態の塩素化有機化合物を効果的に酸化分解できるのは勿論であるが、分解活性が非常に高いために従来の触媒では処理が困難であった粒子態の塩素化有機化合物をも同時に効果的に酸化分解することができる。特に、比表面積および平均細孔径が上述のように設定された多孔質状の担体を用いている場合、粒子態の塩素化有機化合物は、当該担体の特有の多孔質構造のために本発明の触媒に捕捉(吸着)され易くなり、捕捉された状態で効果的に酸化分解され得る。
このため、本発明の塩素化有機化合物分解用触媒をごみ焼却炉や各種の燃焼装置などから発生する排気ガスの処理用触媒として用いると、排気ガス中に含まれるダイオキシン類などの塩素化有機化合物の95%以上を150〜300℃の温度範囲内において5,000hr−1以上の空間速度で酸化分解して無毒性の低分子化合物に転化させ易くなり、結果的に大気中に放出される排気ガス中のダイオキシン類等の濃度を国際毒性等価換算濃度で数ng/Nm3以下に低減させ易くなる。
なお、本発明の触媒が担体として既述のような耐酸化性を有するものを用いている場合、この触媒は、高温雰囲気下で連続的に使用された場合であっても活性が低下しにくく、長期間に渡って塩素化有機化合物に対する安定な分解活性を維持し得る。
以下、本発明を実施例に基づいてより詳細に説明する。
実施例1 コールタールピッチ系活性炭素繊維(平均繊維径=14.0μm、BET比表面積=1,920m2/g、平均細孔径=19.01オングストローム)100gと、30%硝酸水溶液500gとを還流管付きのフラスコに仕込み、硝酸水溶液の沸騰温度で2時間煮沸した。その後、硝酸水溶液から活性炭素繊維を取り出してイオン交換水を用いて十分に洗浄し、120℃で乾燥した。
次に、煮沸処理した活性炭素繊維の全量と、塩化金酸四水和物(HAuCl4・4H2O)3.24g、硝酸鉄(Fe(NO3)3・6H2O)53.13gおよび硝酸ランタン(La(NO3)3・nH2O)11.96gを溶解した水溶液1,000gとをデジタルpH計を取付けたビーカー内に入れた。そして、ビーカー内の溶液を攪拌しながら5重量%の炭酸ナトリウム水溶液を緩やかに滴下し、当該溶液のpHを8.0に設定した。その後、ビーカーから活性炭素繊維を取り出して水で洗浄し、120℃で8時間乾燥した。これにより、金、鉄およびランタンのそれぞれの水酸化物を担持した活性炭素繊維を得た。
次に、上述の水酸化物を担持した活性炭素繊維をセラミック製の管状電気炉内に充填し、450℃の窒素雰囲気中で2時間焼成した後に350℃の水素雰囲気中でさらに1時間還元処理した。これにより、第1触媒成分としての金と、第2触媒成分としての酸化鉄(Fe2O3)および酸化ランタン(La2O3)とが活性炭素繊維上に担持された塩素化有機化合物分解用触媒が得られた。なお、この触媒は、第1触媒成分と第2触媒成分との重量比率(第1触媒成分/第2触媒成分)が7.5/100、第2触媒成分を構成する酸化鉄と酸化ランタンとの重量比率(酸化ランタン/酸化鉄)が30/70、全触媒成分の合計と活性炭素繊維との重量比率(全触媒成分/活性炭素繊維)が13.0/100であった。
このようにして得られた塩素化有機化合物分解用触媒について、o−クロロフェノールに対する酸化分解活性を評価した。ここでは、内容積が113mlのステンレス製反応管(内径19mm×長さ400mm)を用いた流通反応器内に得られた塩素化有機化合物分解用触媒を充填し、この反応器に空間速度4,000hr−1、温度220℃の条件下で3,500ppmのo−クロロフェノールを含有する空気を試料として流した。この際、反応器を通過する前後の試料中のo−クロロフェノール濃度をFID検出器付のガスクロマトグラフを用いて分析し、その分析値から下記の計算式に従ってo−クロロフェノールの分解率を求めた。結果は95.6%であった。
実施例2 実施例1で用いたものと同様のコールタールピッチ系活性炭素繊維100gを実施例1の場合と同様の条件で煮沸処理した。このようにして処理された活性炭素繊維の全量と、塩化金酸四水和物(HAuCl4・4H2O)3.24gおよび硝酸マグネシウム(Mg(NO3)3・6H2O)95.44gを溶解した水溶液1,000gとをデジタルpH計を取付けたビーカー内に入れた。そして、ビーカー内の溶液を攪拌しながら5重量%の炭酸ナトリウム水溶液を緩やかに滴下し、当該溶液のpHを10.2に設定した。その後、ビーカーから活性炭素繊維を取り出して水で洗浄し、120℃で8時間乾燥した。これにより、金およびマグネシウムのそれぞれの水酸化物を担持した活性炭素繊維を得た。
次に、得られた活性炭素繊維を実施例1の場合と同様の条件で窒素雰囲気中および水素雰囲気中で熱処理し、第1触媒成分としての金と、第2触媒成分としての酸化マグネシウム(MgO)とが活性炭素繊維上に担持された塩素化有機化合物分解用触媒を得た。なお、この触媒は、第1触媒成分と第2触媒成分との重量比率(第1触媒成分/第2触媒成分)が6.3/100、全触媒成分の合計と活性炭素繊維との重量比率(全触媒成分/活性炭素繊維)が13.5/100であった。
得られた塩素化有機化合物分解用触媒について、実施例1の場合と同様にしてo−クロロフェノールに対する酸化分解活性を評価したところ、結果は84.3%であった。
実施例3 実施例1で用いたものと同様のコールタールピッチ系活性炭素繊維100gを実施例1の場合と同様の条件で煮沸処理した。このようにして処理された活性炭素繊維の全量と、塩化金酸四水和物(HAuCl4・4H2O)3.24g、硝酸鉄(Fe(NO3)3・9H2O)53.13gおよび硝酸セリウム(Ce(NO3)3・6H2O)11.91gを溶解した水溶液1,000gとをデジタルpH計を取付けたビーカー内に入れた。そして、ビーカー内の溶液を攪拌しながら5重量%の炭酸ナトリウム水溶液を緩やかに滴下し、当該溶液のpHを8.2に設定した。その後、ビーカーから活性炭素繊維を取り出して水で洗浄し、120℃で8時間乾燥した。これにより、金、鉄およびセリウムのそれぞれの水酸化物を担持した活性炭素繊維を得た。
次に、得られた活性炭素繊維を実施例1の場合と同様の条件で窒素雰囲気中および水素雰囲気中で熱処理し、第1触媒成分としての金と、第2触媒成分としての酸化鉄(Fe2O3)および酸化セリウム(CeO2)とが活性炭素繊維上に担持された塩素化有機化合物分解用触媒を得た。なお、この触媒は、第1触媒成分と第2触媒成分との重量比率(第1触媒成分/第2触媒成分)が6.5/100、第2触媒成分を構成する酸化セリウムと酸化鉄の重量比率(酸化セリウム/酸化鉄)が30/70、全触媒成分の合計と活性炭素繊維との重量比率(全触媒成分/活性炭素繊維)が13.7/100であった。
得られた塩素化有機化合物分解用触媒について、実施例1の場合と同様にしてo−クロロフェノールに対する酸化分解活性を評価したところ、結果は93.3%であった。
実施例4 実施例1で用いたものと同様のコールタールピッチ系活性炭素繊維100gを用意した。また、このコールタールピッチ系活性炭素繊維100gの飽和吸水量と同量の水に0.5gのニッケルに相当する酢酸ニッケル((CH3COO)2Ni・4H2O)を溶解して450gの酢酸ニッケル水溶液を調製した。そして、この酢酸ニッケル水溶液にコールタールピッチ系活性炭素繊維を浸漬して攪拌し、当該水溶液の全量をコールタールピッチ系活性炭素繊維に吸収させた。その後、活性炭素繊維を120℃の乾燥器内で8時間乾燥し、活性炭素繊維から水分を除去した。これにより、酢酸ニッケルが分散された活性炭素繊維を得た。
次に、酢酸ニッケルが分散された活性炭素繊維をセラミック製の管状電気炉内に充填し、500℃に設定された100%の水素雰囲気中で4時間エッチング処理した。このようにしてエッチング処理された活性炭素繊維の全量と、塩化金酸四水和物(HAuCl4・4H2O)3.24g、硝酸鉄(Fe(NO3)3・6H2O)53.13gおよび硝酸ランタン(La(NO3)3・6H2O)11.96gを溶解した水溶液1,000gとをデジタルpH計を取付けたビーカー内に入れた。そして、ビーカー内の溶液を攪拌しながら5重量%の炭酸ナトリウム水溶液を緩やかに滴下し、当該溶液のpHを8.0に設定した。その後、ビーカーから活性炭素繊維を取り出して水で洗浄し、120℃で8時間乾燥した。これにより、金、鉄およびランタンのそれぞれの水酸化物を担持した活性炭素繊維を得た。
次に、得られた活性炭素繊維を実施例1の場合と同様の条件で窒素雰囲気中および水素雰囲気中で熱処理し、第1触媒成分としての金と、第2触媒成分としての酸化鉄(Fe2O3)および酸化ランタン(La2O3)とが活性炭素繊維上に担持された塩素化有機化合物分解用触媒を得た。なお、この触媒は、第1触媒成分と第2触媒成分との重量比率(第1触媒成分/第2触媒成分)が8.0/100、第2触媒成分を構成する酸化ランタンと酸化鉄の重量比率(酸化ランタン/酸化鉄)が30/70、全触媒成分の合計と活性炭素繊維との重量比率(全触媒成分/活性炭素繊維)が14.2/100であった。
得られた塩素化有機化合物分解用触媒について、実施例1の場合と同様にしてo−クロロフェノールに対する酸化分解活性を評価したところ、結果は97.7%であった。
実施例5 活性炭素繊維として実施例1の場合と同様に煮沸処理されたものを用いた点を除いて実施例4と同様に操作し、第1触媒成分としての金と、第2触媒成分としての酸化鉄(Fe2O3)および酸化ランタン(La2O3)とが活性炭素繊維上に担持された塩素化有機化合物分解用触媒を得た。なお、この触媒は、第1触媒成分と第2触媒成分との重量比率(第1触媒成分/第2触媒成分)が9.8/100、第2触媒成分を構成する酸化ランタンと酸化鉄の重量比率(酸化ランタン/酸化鉄)が30/70、全触媒成分の合計と活性炭素繊維との重量比率(全触媒成分/活性炭素繊維)が14.9/100であった。
得られた塩素化有機化合物分解用触媒について、実施例1の場合と同様にしてo−クロロフェノールに対する酸化分解活性を評価したところ、結果は99.5%であった。
実施例6 シリカゲル(富士ディビソン株式会社の商品名“シリカゲルB”:粒径=5〜10メッシュ、BET比表面積=450m2/g、平均細孔径=70オングストローム、細孔容積=0.8cc/g)100gと、塩化金酸四水和物(HAuCl4・4H2O)3.24g、硝酸鉄(Fe(NO3)3・6H2O)53.13gおよび硝酸ランタン(La(NO3)3・6H2O)11.96gを溶解した水溶液1,000gとをデジタルpH計を取付けたビーカー内に入れた。そして、ビーカー内の溶液を攪拌しながら5重量%の炭酸ナトリウム水溶液を緩やかに滴下し、当該溶液のpHを8.0に設定した。その後、ビーカーからシリカゲルを取り出して水で洗浄し、120℃で8時間乾燥した。これにより、金、鉄およびランタンのそれぞれの水酸化物を担持したシリカゲルを得た。なお、ここで用いたシリカゲルは、熱分析を実施した場合に150℃以上の温度範囲において相転移点を有するものであり、耐酸化性を有するものであった。
次に、上述の水酸化物を担持したシリカゲルをセラミック製の管状電気炉内に充填し、450℃の空気雰囲気中で2時間焼成した後に350℃の水素雰囲気中でさらに1時間還元処理した。これにより、第1触媒成分としての金と、第2触媒成分としての酸化鉄(Fe2O3)および酸化ランタン(La2O3)とがシリカゲル上に担持された塩素化有機化合物分解用触媒が得られた。なお、この触媒は、第1触媒成分と第2触媒成分との重量比率(第1触媒成分/第2触媒成分)が7.5/100、第2触媒成分を構成する酸化鉄と酸化ランタンとの重量比率(酸化ランタン/酸化鉄)が30/70、全触媒成分の合計と担体であるシリカゲルとの重量比率(全触媒成分/シリカゲル)が8.5/100であった。
得られた塩素化有機化合物分解用触媒について、実施例1の場合と同様にしてo−クロロフェノールに対する酸化分解活性を評価したところ、結果は68.7%であった。
実施例7 アルミナゲル(水澤化学株式会社の商品名“NeobeadD”:粒径=4〜6メッシュ、BET比表面積=320m2/g、平均細孔径=100オングストローム、細孔容積=0.80cc/g)100gと、塩化金酸四水和物(HAuCl4・4H2O)3.24g、硝酸鉄(Fe(NO3)3・6H2O)53.13gおよび硝酸ランタン(La(NO3)3・6H2O)11.96gを溶解した水溶液1,000gとをデジタルpH計を取付けたビーカー内に入れた。そして、ビーカー内の溶液を攪拌しながら5重量%の炭酸ナトリウム水溶液を緩やかに滴下し、当該溶液のpHを8.0に設定した。その後、ビーカーからアルミナゲルを取り出して水で洗浄し、120℃で8時間乾燥した。これにより、金、鉄およびランタンのそれぞれの水酸化物を担持したアルミナゲルを得た。なお、ここで用いたアルミナゲルは、熱分析を実施した場合に150℃以上の温度範囲において相転移点を有するものであり、耐酸化性を有するものであった。
次に、上述の水酸化物を担持したアルミナゲルをセラミック製の管状電気炉内に充填し、450℃の空気雰囲気中で2時間焼成した後に350℃の水素雰囲気中でさらに1時間還元処理した。これにより、第1触媒成分としての金と、第2触媒成分としての酸化鉄(Fe2O3)および酸化ランタン(La2O3)とがアルミナゲル上に担持された塩素化有機化合物分解用触媒が得られた。なお、この触媒は、第1触媒成分と第2触媒成分との重量比率(第1触媒成分/第2触媒成分)が7.5/100、第2触媒成分を構成する酸化鉄と酸化ランタンとの重量比率(酸化ランタン/酸化鉄)が30/70、全触媒成分の合計と担体であるアルミナゲルとの重量比率(全触媒成分/アルミナゲル)が9.9/100であった。
得られた塩素化有機化合物分解用触媒について、実施例1の場合と同様にしてo−クロロフェノールに対する酸化分解活性を評価したところ、結果は76.5%であった。
実施例8 粒状活性炭(武田薬品工業株式会社の商品名“WH2C−20/48”:粒径=20〜48メッシュ、BET比表面積=1,476m2/g、平均細孔径=15.6オングストローム、細孔容積=0.64cc/g)100gと、塩化金酸四水和物(HAuCl4・4H2O)3.24g、硝酸鉄(Fe(NO3)3・6H2O)53.13gおよび硝酸ランタン(La(NO3)3・6H2O)11.96gを溶解した水溶液1,000gとをデジタルpH計を取付けたビーカー内に入れた。そして、ビーカー内の溶液を攪拌しながら5重量%の炭酸ナトリウム水溶液を緩やかに滴下し、当該溶液のpHを8.0に設定した。その後、ビーカーから粒状活性炭を取り出して水で洗浄し、120℃で8時間乾燥した。これにより、金、鉄およびランタンのそれぞれの水酸化物を担持した粒状活性炭を得た。
次に、上述の水酸化物を担持した粒状活性炭をセラミック製の管状電気炉内に充填し、450℃の窒素雰囲気中で2時間焼成した後に350℃の水素雰囲気中でさらに1時間還元処理した。これにより、第1触媒成分としての金と、第2触媒成分としての酸化鉄(Fe2O3)および酸化ランタン(La2O3)とが粒状活性炭上に担持された塩素化有機化合物分解用触媒が得られた。なお、この触媒は、第1触媒成分と第2触媒成分との重量比率(第1触媒成分/第2触媒成分)が7.5/100、第2触媒成分を構成する酸化鉄と酸化ランタンとの重量比率(酸化ランタン/酸化鉄)が30/70、全触媒成分の合計と担体である粒状活性炭との重量比率(全触媒成分/粒状活性炭)が11.2/100であった。
得られた塩素化有機化合物分解用触媒について、実施例1の場合と同様にしてo−クロロフェノールに対する酸化分解活性を評価したところ、結果は89.0%であった。
実施例9 粉末状活性炭(大阪瓦斯株式会社の商品名“M−30”:平均粒径=10μm、BET比表面積=3,400m2/g、平均細孔径=10.5オングストローム、細孔容積=1.79cc/g)100gと、塩化金酸四水和物(HAuCl4・4H2O)3.24g、硝酸鉄(Fe(NO3)3・6H2O)53.13gおよび硝酸ランタン(La(NO3)3・6H2O)11.96gを溶解した水溶液1,000gとをデジタルpH計を取付けたビーカー内に入れた。そして、ビーカー内の溶液を攪拌しながら5重量%の炭酸ナトリウム水溶液を緩やかに滴下し、当該溶液のpHを8.0に設定した。その後、ビーカーから粉末状活性炭を取り出して水で洗浄し、120℃で8時間乾燥した。これにより、金、鉄およびランタンのそれぞれの水酸化物を担持した粉末状活性炭を得た。
次に、上述の水酸化物を担持した粉末状活性炭をセラミック製の管状電気炉内に充填し、450℃の窒素雰囲気中で2時間焼成した後に350℃の水素雰囲気中でさらに1時間還元処理した。これにより、第1触媒成分としての金と、第2触媒成分としての酸化鉄(Fe2O3)および酸化ランタン(La2O3)とが粉末状活性炭上に担持された塩素化有機化合物分解用触媒が得られた。なお、この触媒は、第1触媒成分と第2触媒成分との重量比率(第1触媒成分/第2触媒成分)が7.5/100、第2触媒成分を構成する酸化鉄と酸化ランタンとの重量比率(酸化ランタン/酸化鉄)が30/70、全触媒成分の合計と担体である粉末状活性炭との重量比率(全触媒成分/粉末状活性炭)が16.5/100であった。
得られた塩素化有機化合物分解用触媒について、実施例1の場合と同様にしてo−クロロフェノールに対する酸化分解活性を評価したところ、結果は100%であった。
実施例10 活性白土(平均粒径=3mm、BET比表面積=200m2/g、細孔分布=20〜75,000オングストローム)100gと、塩化金酸四水和物(HAuCl4・4H2O)3.24g、硝酸鉄(Fe(NO3)3・6H2O)53.13gおよび硝酸ランタン(La(NO3)3・6H2O)11.96gを溶解した水溶液1,000gとをデジタルpH計を取付けたビーカー内に入れた。そして、ビーカー内の溶液を攪拌しながら5重量%の炭酸ナトリウム水溶液を緩やかに滴下し、当該溶液のpHを8.0に設定した。その後、ビーカーから活性白土を取り出して水で洗浄し、120℃で8時間乾燥した。これにより、金、鉄およびランタンのそれぞれの水酸化物を担持した活性白土を得た。なお、ここで用いた活性白土は、熱分析を実施した場合に150℃以上の温度範囲において相転移点を有するものであり、耐酸化性を有するものであった。
次に、上述の水酸化物を担持した活性白土をセラミック製の管状電気炉内に充填し、450℃の空気雰囲気中で2時間焼成した後に350℃の水素雰囲気中でさらに1時間還元処理した。これにより、第1触媒成分としての金と、第2触媒成分としての酸化鉄(Fe2O3)および酸化ランタン(La2O3)とが活性白土上に担持された塩素化有機化合物分解用触媒が得られた。なお、この触媒は、第1触媒成分と第2触媒成分との重量比率(第1触媒成分/第2触媒成分)が7.5/100、第2触媒成分を構成する酸化鉄と酸化ランタンとの重量比率(酸化ランタン/酸化鉄)が30/70、全触媒成分の合計と担体である活性白土との重量比率(全触媒成分/活性白土)が9.3/100であった。
得られた塩素化有機化合物分解用触媒について、実施例1の場合と同様にしてo−クロロフェノールに対する酸化分解活性を評価したところ、結果は92.0%であった。
実施例11 図1に示すような、排気ガス分解処理塔を備えたゴミ焼却装置を建設した。図において、ゴミ焼却装置1は、焼却炉2、排気ガス分解処理塔3、および焼却炉2と排気ガス分解処理塔3とを連結するための排気ガス流路4を主に備えている。
焼却炉2は、1次焼却炉5と、その上部に配置された2次焼却炉6とを備えている。1次焼却炉5は、ゴミ20を焼却するための燃焼室7を有しており、燃焼室7には2次焼却炉6に向けて排気路8が連結している。2次焼却炉6は、一端が排気路8に連結された塔状に構成されており、排気路8側から順に再燃バーナー9、セラミックチェッカー10、2次燃焼室11およびエジェクター送風機12を備えている。
排気ガス分解処理塔3は、触媒を充填するための触媒室13を備えており、そこには排気ガスの流入路14と流出路15とが接続されている。また、流入路14および流出路15には、それぞれ排気ガスを採取するための採取口16、17が設けられている。
排気ガス流路4は、一端が焼却炉2の2次焼却炉6に連結されかつ他端が排気ガス分解処理塔3の流入路14に連結されており、水噴霧冷却塔18を有している。
このようなゴミ焼却装置1において、燃焼室7でゴミ20を焼却する際に発生する排気ガスは、排気路8を通って2次焼却炉6内に導かれ、そこの再燃バーナー9により更に燃焼されてから排気ガス流路4内に流入する。排気ガス流路4内に導入された排気ガスは、水噴霧冷却塔18により冷却された後に排気ガス分解処理塔3内に導かれ、その触媒室13で分解処理された後に流出路15から外部に放出される。
この実施例では、上述のゴミ焼却装置1の触媒室13内に実施例5で得られた塩素化有機化合物分解用触媒を充填して実際に都市ゴミを焼却し、表1に示す条件下における排気ガス中のダイオキシン類の酸化分解状況を調べた。この際、試料となる排気ガスは、触媒室13での処理前のものは採取口16から採取し、処理後のものは採取口17から採取した。また、試料の採取方法および分析方法は、平成9年2月26日衛生第38号に記載されている日本国厚生省が規定した「廃棄物処理におけるダイオキシン類標準測定分析指針マニュアル」に従った。さらに、排気ガス中の酸素濃度、排気ガス温度および排気ガス流量の測定は、それぞれ日本工業規格JIS K0301−1989に規定された「排気ガス中の酸素測定方法」のうちのジルコニア方式、JIS Z8808−1995に規定された「排気ガス中のダスト濃度の測定方法」のうちのKタイプ熱電対方式、およびJIS Z8808−1995に規定された「排気ガス中のダスト濃度の測定方法」のうちのピトー管方式に従った。
触媒室13の入口側と出口側でそれぞれ採取した排気ガス中に含まれるガス態および粒子態のダイオキシン類の濃度の測定結果、およびダイオキシン類の除去率を表2(表2−1および表2−2)に示す。
なお、表2中、塩素化有機化合物を示す各略号は下記の化合物を示している。また、表2中の”TEF”は、毒性等価係数である。
T4CDD:四塩化ジベンゾダイオキシンT4CDDs:四塩化ジベンゾダイオキシン類P5CDD:五塩化ジベンゾダイオキシンP5CDDs:五塩化ジベンゾダイオキシン類H6CDD:六塩化ジベンゾダイオキシンH6CDDs:六塩化ジベンゾダイオキシン類H7CDD:七塩化ジベンゾダイオキシンH7CDDs:七塩化ジベンゾダイオキシン類O8CDD:八塩化ジベンゾダイオキシンPCDDs:ポリ塩化ジベンゾ・パラ・ダイオキシン類T4CDF:四塩化ジベンゾフランT4CDFs:四塩化ジベンゾフラン類P5CDF:五塩化ジベンゾフランP5CDFs:五塩化ジベンゾフラン類H6CDF:六塩化ジベンゾフランH6CDFs:六塩化ジベンゾフラン類H7CDF:七塩化ジベンゾフランH7CDFs:七塩化ジベンゾフラン類O8CDF:八塩化ジベンゾフランPCDFs:ポリ塩化ジベンゾフラン類OCDDs:八塩化ジベンゾダイオキシン類 表2から明らかなように、実施例5の塩素化有機化合物分解用触媒を用いると、排気ガス中に含まれるガス態のダイオキシン類の概ね98%を除去でき、また、当該排気ガス中に含まれる粒子態のダイオキシン類も概ね96%が除去できたことがわかる。
実施例12 実施例5で得られた塩素化有機化合物分解用触媒に代えて実施例6で得られた塩素化有機化合物分解用触媒を用い、実施例11の場合と同様にして排気ガス中のダイオキシン類の酸化分解状況を調べた。結果を表3(表3−1および表3−2)に示す。なお、表3において、塩素化有機化合物を示す各略号および“TEF”は、表2の場合と同じである。
実施例13 実施例5で得られた塩素化有機化合物分解用触媒に代えて実施例7で得られた塩素化有機化合物分解用触媒を用い、実施例11の場合と同様にして排気ガス中のダイオキシン類の酸化分解状況を調べた。結果を表4(表4−1および表4−2)に示す。なお、表4において、塩素化有機化合物を示す各略号および“TEF”は、表2の場合と同じである。
実施例14 実施例5で得られた塩素化有機化合物分解用触媒に代えて実施例8で得られた塩素化有機化合物分解用触媒を用い、実施例11の場合と同様にして排気ガス中のダイオキシン類の酸化分解状況を調べた。結果を表5(表5−1および表5−2)に示す。なお、表5において、塩素化有機化合物を示す各略号および“TEF”は、表2の場合と同じである。
実施例15 実施例5で得られた塩素化有機化合物分解用触媒に代えて実施例9で得られた塩素化有機化合物分解用触媒を用い、実施例11の場合と同様にして排気ガス中のダイオキシン類の酸化分解状況を調べた。結果を表6(表6−1および表6−2)に示す。なお、表6において、塩素化有機化合物を示す各略号および“TEF”は、表2の場合と同じである。
実施例16 実施例5で得られた塩素化有機化合物分解用触媒に代えて実施例10で得られた塩素化有機化合物分解用触媒を用い、実施例11の場合と同様にして排気ガス中のダイオキシン類の酸化分解状況を調べた。結果を表7(表7−1および表7−2)に示す。なお、表7において、塩素化有機化合物を示す各略号および“TEF”は、表2の場合と同じである。
本発明は、その精神または主要な特徴から逸脱することなく、他のいろいろな形で実施することができる。そのため、上述の実施例はあらゆる点で単なる例示に過ぎず、限定的に解釈してはならない。本発明の範囲は、請求の範囲によって示すものであって、明細書本文にはなんら拘束されない。さらに、請求の範囲の均等範囲に属する変形や変更は、すべて本発明の範囲内のものである。
【図面の簡単な説明】
図1は、実施例11〜16で用いたゴミ焼却装置の概略図である。