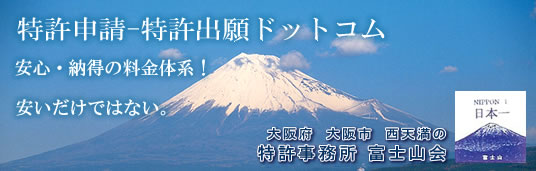
超音波深傷装置
(書誌+要約+請求の範囲)
(19)【発行国】日本国特許庁(JP)
(12)【公報種別】公開特許公報(A)
(11)【公開番号】特開平6−317567
(43)【公開日】平成6年(1994)11月15日
(54)【発明の名称】超音波探傷装置
(51)【国際特許分類第5版】
G01N 29/04 502 8105-2J
29/10 501 6928-2J
【審査請求】有
【請求項の数】1
【出願形態】OL
【全頁数】6
(21)【出願番号】特願平3−230617
【出願変更の表示】実願平3−60458の変更
(22)【出願日】平成3年(1991)7月31日
(71)【出願人】
【識別番号】000000284
【氏名又は名称】大阪瓦斯株式会社
【住所又は居所】大阪府大阪市中央区平野町四丁目1番2号
(71)【出願人】
【識別番号】000235532
【氏名又は名称】非破壊検査株式会社
【住所又は居所】大阪府大阪市北区西天満2丁目10番2号
(72)【発明者】
【氏名】中西 準二
【住所又は居所】大阪市中央区平野町四丁目1番2号 大阪瓦斯株式会社内
(72)【発明者】
【氏名】高橋 英夫
【住所又は居所】大阪市中央区平野町四丁目1番2号 大阪瓦斯株式会社内
(72)【発明者】
【氏名】佐藤 富徳
【住所又は居所】大阪市中央区平野町四丁目1番2号 大阪瓦斯株式会社内
(72)【発明者】
【氏名】片山 強
【住所又は居所】大阪市中央区北久宝寺町2丁目3番6号 非破壊検査株式会社内
(72)【発明者】
【氏名】大畠 克範
【住所又は居所】大阪市中央区北久宝寺町2丁目3番6号 非破壊検査株式会社内
(72)【発明者】
【氏名】境 英明
【住所又は居所】大阪市中央区北久宝寺町2丁目3番6号 非破壊検査株式会社内
(74)【代理人】
【弁理士】
【氏名又は名称】西教 圭一郎
(57)【要約】
【目的】 管材や板材の表面付近の欠陥を、広い範囲でS/N比が高い状態で検出する。
【構成】 探触子11には、送信用の振動子12と受信用の振動子13が1ストロークの間隔bだけ離して取付けられる。振動子12,13は、くさび14,15によって同一角度だけ傾斜して取付けられる。超音波は、材料10中に、屈折角θで入射点30から入射する。材料10中で、超音波は、屈折角θで反射しながら進行し、割れ20に達する。超音波は割れ20で反射して戻り、出射点34に到達して、くさび15を通過して受信用の振動子13に到達する。表示器21では、受信用の振動子13からの出力のピークから、割れ20までの距離を推定する。
【特許請求の範囲】
【請求項1】 探触子本体と、探触子本体に傾斜して取付けられ、予め定める一定の屈折角で探傷すべき材料中に超音波を送信する送信素子と、探傷すべき材料の内外表面間を前記屈折角で全反射して伝搬する超音波を受信できる間隔だけ、送信方向と反対側に送信素子から離して、探触子本体に送信素子と同一傾斜角で取付けられる受信素子とを含むことを特徴とする超音波探傷装置。
詳細な説明
【発明の詳細な説明】
【0001】
【産業上の利用分野】本発明は、配管、板等の内外面の表面近傍にある微少な割れなどの欠陥を検出する超音波探傷装置に関する。
【0002】
【従来の技術】都市ガス配管系統に使用される管材においては、割れなどの欠陥が生じると、ガス漏れが生じたり、管が破損してガスが大量に噴出したりして、非常に危険である。そのため、割れなどの欠陥は、できるだけ初期のうちに発見し、危険防止のための処置を施すことが必要である。ガスなどの供給に実際に使用中の管材などの割れを検出する方法としては、超音波探傷法が用いられる。超音波探傷法においては、管材中に超音波を送信し、割れなどの欠陥部分において反射される超音波を受信して、その反射強度から割れの大きさなどの情報を得る。
【0003】図8は、従来からの超音波探傷法の一例を示す。ガス管などの材料1の表面付近には、割れ2が存在する。割れ2に対して一定の関係を有する位置に探触子3が配置されると、割れ2の検出が可能となる。探触子3には、振動子4がくさび5によって傾斜して取付けられる。くさび5中には、ビーム中心6で示すように超音波が進行し、材料1中に入射する時点で屈折角θ1を有するように屈折する。屈折角θ1を有するように屈折した超音波ビームは、材料1の他方表面で全反射し、割れ2に達する。割れ2に到達した超音波は、反対方向に反射され、振動子4に戻る。したがって、振動子4を一定時間だけ振動させた後で、振動子4からの超音波の送信を停止し、振動子4によって割れ2から反射した超音波の振動を受信する。振動子4は圧電効果や磁歪効果によって、外部から与えられる電気エネルギを超音波エネルギに変換し、また超音波エネルギを電気エネルギに変換する。振動子4へのエネルギの供給または振動子4からの受信情報は、リード線7を介して探傷ケーブル8に与えられる。探触子3のケースとくさび5との間には、吸音材9が充填される。
【0004】図9は、図8図示の探触子3によって材料1中の割れ2を検出するときの振動子4が受信する超音波の強度変化を示す。振動子4から超音波が送信されると、くさび5中をビーム中心6に沿って進み、くさび5と材料1との界面で屈折角θ1となるように屈折して材料1中に入射する。この振動子4は、超音波の送信が終了すると直ちに受信に切換えられるけれども、機械的な振動状態が減衰するまでに時間を要し、時刻t1まではかなり大きな振動が残る。材料1中で超音波は反射角θ1で全反射しながら伝搬し、割れ2に到達する。割れ2では超音波の一部が反射され、逆方向に進行して時刻tにおいて振動子4に到達する。
【0005】
【発明が解決しようとする課題】従来からの図8図示の構成によれば、図9図示のような出力が得られ、材料1中の割れ2からの反射波のピーク位置tから割れ2までの距離b1を計算することができる。
【0006】すなわち、tの時刻までに超音波は入射点から割れ2まで往復しているので、片道に要する時間はtの半分となる。材料1中で超音波は、屈折角θ1だけ傾斜して音速c1で進行するものとすると、次の数1の式が得られる。
【0007】
【数1】b1=0.5×t×c1×sinθ1従来からの図8のような構成による割れ2の検出においては、割れ2までの距離b1が数1の式のようにして計算することができ、しかもいずれの表面側にあるのか、あるいは材料1の内部にあるのかを判断することができる。しかしながら、図9に示すように、時刻t1までの間は振動子4が正常に割れ2からの反射波を受信することはできない。すなわち、このような不感帯によって短い距離の欠陥を検出することはできない。また、時刻tにおけるピーク時と、周囲のノイズレベルとの比であるS/N比は、一定条件の試験片による実験結果では、約2.7と比較的低い値となる。
【0008】実際に超音波探傷装置を使用する目的としては、管材などに応力腐食割れが生じているか否かを検出することが重要である。応力腐食割れは、材料中に残留する応力の存在と、腐食性の雰囲気の相乗効果によって促進される。材料中の応力の残留は、たとえば溶接を行った付近の、いわゆる熱影響部で顕著となる。応力腐食割れを防止するためには、少なくとも溶接部付近を厳重に塗装する必要がある。たとえば、材料がオーステナイト系ステンレス鋼であるSUS304など、一般的には耐蝕性が良い材料であっても、塩素雰囲気では応力腐食割れを起こし易いので、特に溶接部付近では塗装が必要である。超音波探傷装置を使用するとき、塗装被膜を介して超音波を送受信すると、S/N比が60〜80%に低下する。図9に示すように、S/N比が2.7程度であれば、信号とノイズとの判別は比較的容易といえるけれども、この60%程度になると判別は困難となる。したがって従来からの図8図示のような構成によっては、塗装膜が施されている材料に対して十分な探傷を行うことができない。
【0009】本発明の目的は、簡単な構成で、広い範囲の欠陥を良好なS/N比で検出することができる超音波探傷装置を提供することである。
【0010】
【課題を解決するための手段】本発明は、探触子本体と、探触子本体に傾斜して取付けられ、予め定める一定の屈折角で探傷すべき材料中に超音波を送信する送信素子と、探傷すべき材料の内外表面間を前記屈折角で全反射して伝搬する超音波を受信できる間隔だけ、送信方向と反対側に送信素子から離して、探触子本体に送信素子と同一傾斜角で取付けられる受信素子とを含むことを特徴とする超音波探傷装置である。
【0011】
【作用】本発明に従えば、送信素子は探触子本体に傾斜して取付けられる。送信素子からは、予め定める一定の屈折角で探傷すべき材料中に超音波を送信する。材料の内外表面間を前記屈折角で全反射して材料中を伝搬する超音波は、割れなどの欠陥部で反射して進行路を逆方向に戻る。この伝搬方向、すなわち送信方向と反対側に送信素子から離れて受信素子が送信素子と同一傾斜角を有して配置される。その距離は、送信素子に到達する反射波が、さらに材料の内外表面間を前記屈折角で全反射して伝搬する距離であるので、受信素子には割れなどの欠陥によって反射した超音波が受信される。送信素子と受信素子とが分離しているので、受信素子には不感帯はほとんど生じない。また、送信素子と受信素子との距離は、超音波が材料の内外表面を全反射して伝搬する距離であるので、異なった角度で進行する超音波は受信素子に到達せず、雑音の少ない状態で欠陥の検出を行うことができる。
【0012】
【実施例】図1は、本発明の一実施例による超音波探傷装置の電気的構成を示すブロック図である。管材や板材などの材料10の表面には、探触子11が接触する。探触子11中には、送信素子である送信用の振動子12と、受信素子である受信用の振動子13とが分離して収納される。送信用の振動子12は、くさび14に取付けられる。振動子12,13はダンパ16,17によってそれぞれ制動される。探触子11内の空間には吸音材18が充填される。探触子11の本体であるケース内は、音響仕切板19によって送信用および受信用の区画に分離される。
【0013】振動子12,13は、同一形状で、同一共振周波数、たとえば5MHzを有する。振動子4の材料としては、たとえばチタン酸バリウムなどの磁器材料が用いられる。くさび14,15も同一形状であり、材料としてはアクリル樹脂などが用いられる。くさび14,15は、材料10中で超音波が屈折角θ、たとえば45°を有するように、振動子12,13を傾斜して保持する。ダンパ16,17は、布入りのフェノール樹脂などが用いられ、振動子12,13の余分な振動を防止する。吸音材18は、空気を介して超音波が伝搬するのを防止し、音響仕切板19は、送信部と受信部とを音響的に分離する。以上のように、振動子12,13に関連する構造はほぼ同一であるので、探触子11の製造は容易で、コストダウンが可能である。
【0014】材料中に存在する割れ20などの欠陥は、表示器21による表示によって検出される。この検出を行うために、発振器22から5MHzの信号出力が送信用の振動子12に与えられる。表示器21および発振器22は、探傷器23に含まれる。発信器からの信号出力は、発振器22から振動子12に対してコネクタ24を介して与えられる。受信用の振動子13からの信号出力は、コネクタ25を介して表示器21に与えられる。
【0015】送信用の振動子12から送信された超音波は、くさび14中を進み、材料10の表面で入射点30に達する。材料10中では、屈折角θとなるように屈折して、入射点30側の表面と対向する側の表面の反射点31に達する。反射点31では、表面が空気と接触しており、空気中の音速はくさび14,15中の音速よりも小さいので、材料10中の音速との差が大きく、超音波は反射点31で全反射され、割れ20の反射点32に達する。反射点32では、超音波の進行方向が逆転され、反射点31を経て入射点30に戻る。入射点30では、さらに反射して反射点33で再び全反射し、出射点34に達する。出射点34では、到達した超音波の一部がくさび15中に侵入し、受信用の振動子13に到達する。入射点30と出射点34との距離bは、超音波が屈折角θで1回全反射して到達する1スキップの距離である。この距離は、たとえば屈折角θが45°のときには、板厚aの2倍となる。一般には、距離bを次の数2の式で表されるように選ぶ。
【0016】
【数2】b=n×2a×tanθ)
ここで、n=1,2,3,…である。
【0017】割れ20までの距離は、材料10中の音速と屈折角θによって求めることができる。割れ20が検出されたかどうかは、その距離だけ離れた表面を押さえるなどして、表示器21の表示が変化するか否かで判断することができる。
【0018】図2は、図1図示の探触子11の平面図である。この探触子11の本体に取付けられる、送信素子である送信用の振動子12と受信素子である受信用の振動子13との間隔は、上述のように1スキップに選ぶのが望ましいけれども、板厚aが薄いときには、1スキップの整数倍、たとえば3スキップ程度であっても差支えないことが、実験結果により確認されている。
【0019】図3は、欠陥による反射の状態を示す。図3Aは、反射点32から少しずれた位置に割れ20が存在し、超音波の往路と復路とが少しだけずれる状態を示す。すなわち往路35を経て反射点32に到達した超音波は、全反射して36の方向に進み、割れ20で反射して復路37の方向に戻る。参照符36で示す行程が短かければ、往路35と復路37のずれは小さく、図1図示の探触子11で割れ20の検出は十分可能である。図3Bは、割れ20が、材料10の結晶粒界38に沿って、表面に対して傾斜して発生する状態を示す。この状態の方が、むしろ往路35と復路37とのずれが小さくなる。本実施例によれば、以上のように、割れ20が材料10の表面に垂直な場合のみならず、傾斜している場合でも、その検出が可能である。
【0020】図4は、図1図示の実施例の動作を確認するための試験片40の形状を示す。試験片40には、予め人工的な欠陥である溝A,B,C,D,Eが設けられている。
【0021】図5は、図9図示の結果を得たと同一の試験片(欠陥E)による図1図示の実施例による超音波探傷の結果を示す。注目すべきは、不感帯がなく、時刻tにおける信号のピークが高くなってノイズが減少し、S/N比が約5.5と向上していることである。
【0022】図6は、図4図示の試験片40を用いる試験の状態を示す。記録器41はAC電源コード42から電力を供給される。試験片40には治具43が取付けられ、探触子11の角度を変えて、人工的な欠陥A,B,C,D,Eからの距離を変えることができる。この検出結果を表1に示す。
【0023】
【表1】
【0024】本試験は、各試験片に直径2.4mmの縦穴を空け、3.0スキップ離れた位置の探触子11による検出ピークが、50%となるように感度を調整して行っている。表1の結果で塗装前のS/N比は十分に高く、さらに試験片に塗装を施した後でもS/N比は比較的高い値が得られる。
【0025】図7は、材料10に溶接部50が設けられ、その周囲の熱影響部51の付近に、塗装膜52が設けられている状態を示す。都市ガスは、液化天然ガス(略称「LNG」)を原料の1つとして用いている。LNG工場内の配管材料には、低温脆性を示さないオーステナイト系ステンレス鋼のSUS304などの材料による管材が使用されている。このような管材は、通常時は常温であるけれども、緊急時にLNGが流れて低温となる場合がある。そのような熱衝撃が加わったときに、割れなどが生じていると危険である。ステンレス鋼は一般的には耐蝕性が良好であるけれども、海岸付近の塩素リッチな環境化では応力腐食割れが発生するおそれがある。したがって、安全性を確保するために、完全な防食構造とする必要があり、塩素から遮断するための塗装が必要である。しかしながら、この塗装被膜は、応力腐食割れを検査するためには障害となる。図8図示の従来からの構成で超音波探傷を行うためには、塗装膜52を除去しなければならない。防食のための塗装膜を除去して、信頼性確保のための検査を行うことは、検査のためにかえって腐食の危険性を増大する結果ともなりかねない。したがって、検査後には再度厳重な塗装を行う必要がある。表1の結果によれば、図1図示の実施例を用いて、塗装を施したままで十分な超音波探傷を行うことができる。
【0026】
【発明の効果】以上のように本発明によれば、不感帯をほとんど生じることなく、しかも高いS/N比で割れなどの欠陥の検出を行うことができる。S/N比が高いので、探傷すべき材料の表面に塗装膜が施されていても欠陥の検出が可能となる。実際に使用中の管材などでは、応力腐食割れを防止するために塗装を施しているけれども、欠陥を検出するために塗装の剥離を行う必要もない。
【0027】また、送信素子と受信素子とは同一傾斜角で取付けられるので、超音波探触子の製造が簡素化されてコストダウンとなる。